Spis treści
Jeden z największych producentów baterii cynkowo-węglowych w Europie, w ramach podnoszenia poziomu bezpieczeństwa w zakładzie, zwrócił się do inżynierów CORONA Serwis. Zadanie polegało na stworzeniu koncepcji zabezpieczenia przeciwwybuchowego układu technologicznego na jednej z linii produkujących baterie alkaliczne.
Do produkcji baterii alkalicznych wykorzystuje się różnego rodzaju surowce. Niektóre z nich wykazują właściwości palne i/lub wybuchowe. Należą do nich m.in. grafit i propylen, które klasyfikuje się w grupie pyłów ST1. Stąd bardzo ważne jest odpowiednie zabezpieczenie procesów, w których te pyły się pojawiają.
Produkcja baterii – trudny proces wymagający sprawdzonych zabezpieczeń
Proces produkcyjny baterii rozpoczyna się od zasypywania ręcznego surowców. Przeważnie czynności te wykonywane przez kadrę pracowniczą, gdzie z worków o wskazanej pojemność wysypuje się surowiec do przeznaczonego do tego, obudowanego i odpylanego układu zasypowego. Z układu zasypowego, z reguły przez dozownik celkowy i rurociąg transportu pneumatycznego, surowiec trafia do filtrocyklonu. Tam, oczyszczone powietrze z filtrocyklonu wentylator odprowadza na zewnątrz budynku/hali produkcyjnej.
W opisanym powyżej procesie podawania surowców występują obszary, które zaliczyć można do zagrożonych wybuchem. Wynika to z charakterystyki tego procesu i właściwości wybuchowych samego surowca.
Dlatego w takim układzie technologicznym w pierwszej kolejności inżynierowie CORONA Serwis zabezpieczyli filtrocyklon, który znajduje się w hali. Przede wszystkim urządzenie zabezpieczono za pomocą systemów aktywnych – tłumienia butli HRD. Ponadto, rurociągi transportujące surowiec zostały doposażone w system odsprzęgania wybuchu za pomocą butli SRD. Zastosowany system przeciwwybuchowy chroni zarówno samo urządzenie (butla HRD), jak również izoluje układ (butla SRD) od pozostałej części instalacji technologicznej.
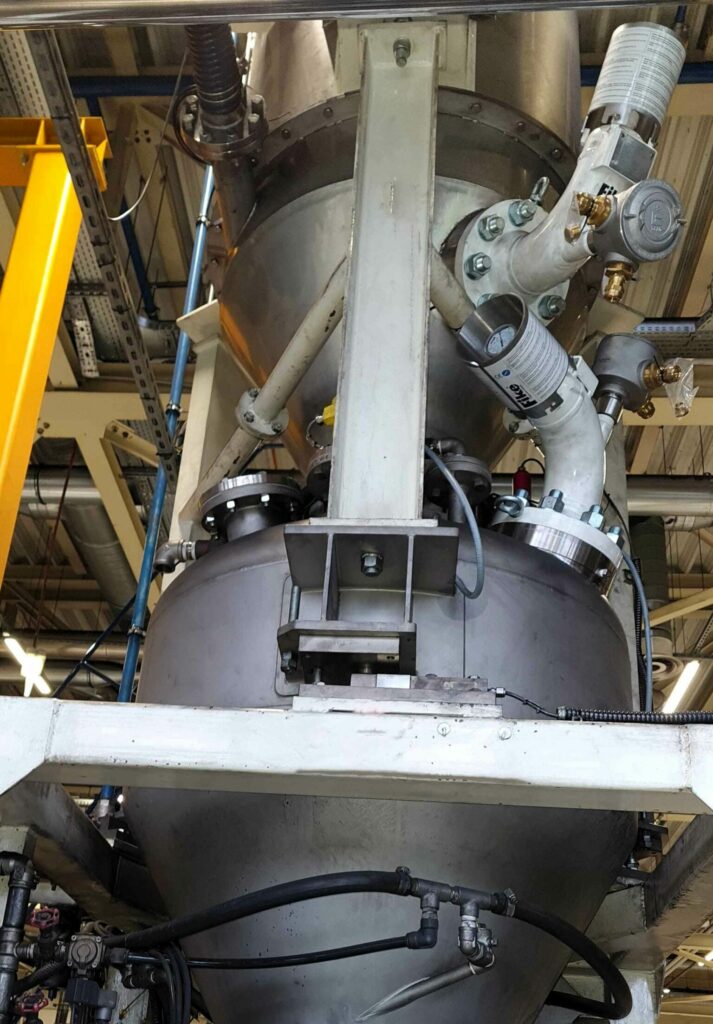
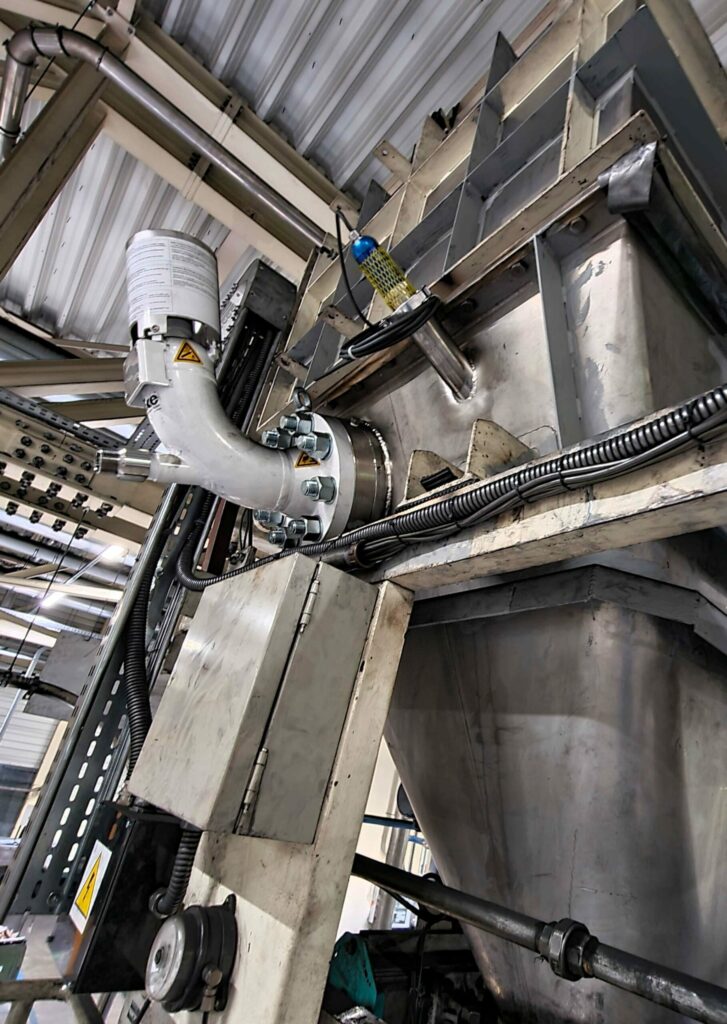
Zabezpieczenie filtrocyklonu ze zbiornikiem wagowym za pomocą HRD i SRD
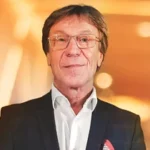
Filtrocyklony, bardzo często w tego typu układach technologicznych, zabudowane są bezpośrednio na zbiornikach wagowych o różnych pojemnościach. Do nich, poprzez pneumatycznie sterowane przepustnice, dozowane są odpowiednie ilości danego surowca. Dozowanie surowców np. polietylenu, realizowane jest przenośnikiem ślimakowym, zabudowanym na wysypie z pojemnika wagowego polietylenu. W układzie dozowania polietylenu występują połączenia kompensacyjne, które oczywiście gwarantują szczelność procesu. Wynikiem tego jest brak zalegających warstw pyłu. Jednak układ urządzeń filtrocyklon – zbiornik wagowy, wymaga odpowiedniego systemu ochronnego. W tym przypadku nasi inżynierowie zastosowali system aktywny w postaci butli HRD i SRD
— Wiesław Jobczyk, prezes zarządu CORONA Serwis.
Analizując proces dalej należy zwrócić uwagę na odważone w zbiornikach wagowych surowce, które w odpowiednich proporcjach transportowane są pneumatycznie do mieszalnika. Na mieszalniku zabudowano cyklon odbierający oraz filtr workowy. Oczyszczone powietrze z filtra odprowadza się ponad dach budynku, do atmosfery. Mieszalnik oraz filtr workowy ze względu na swoje umiejscowienie w hali produkcyjnej zostały zabezpieczone układem butli HRD. Do koniecznej izolacji wybuchu na rurociągach inżynierowie CORONA Serwis zastosowali zawór szybkozamykający typu FAV.