Czym jest silos?
Silos to pionowy magazyn, w którym przechowuje się m.in. zboże w celu zachowania jego jakości i zapewnienia stałej podaży. Silosy są powszechnie stosowane w różnych gałęziach przemysłu, w szczególności dotyczy to przemysłu spożywczego, rolniczego, drzewno-papierniczego czy gałęzi przemysłu ciężkiego w tym m.in. chemicznego, metalurgicznego lub energetycznego. Konstrukcja silosów może osiągać wysokość dochodzącą nawet do kilkudziesięciu metrów a ich pojemność może wynosić nawet kilka tysięcy ton. Dzięki temu, przechowywanie znacznych ilości materiałów sypkich nie stanowi problemu.
Silosy zbożowe wyposażone są w systemy wentylacyjne i grzewcze, co pozwala na kontrolowanie wilgotności oraz temperatury powietrza wewnątrz zbiornika. Dzięki temu możliwe jest przechowywanie np. ziarna przez długi czas, bez ryzyka jego zepsucia. Stąd tak chętnie i głównie wykorzystywane są w przemyśle rolniczo-spożywczym.
Należy pamiętać, że jeżeli np. ziarno jest zbyt wilgotne, może pojawić się pleśń, co prowadzi do strat w plonach. Natomiast jeżeli temperatura jest zbyt wysoka może to spowodować utratę wartości odżywczych składowanych ziaren. Dlatego tak ważny jest odpowiedni dobór paramentów i wyposażenia silosu uwzględniających charakterystykę przechowywanego surowca.
Z czego składa się silos?
Silos składa się z kilku podstawowych elementów. Do najważniejszych zaliczyć można: zewnętrzną obudowę, wewnętrzny pojemnik, system wentylacji, włazy, a także systemy dozowania i transportu materiałów. Zewnętrzna obudowa zazwyczaj wykonana jest z metalu, a wewnętrzny pojemnik często posiada stożkową lub cylindryczną formę. Często silosy są w odpowiedni sposób oczujnikowane np. kontrola temperatury, kontrola wilgotności, kontrola poziomu zasypu etc.
Jakie są rodzaje silosów?
W zależności od produktu, który ma być przechowywany wewnątrz oraz od wymagań dotyczących jego przechowywania i transportu, wyróżniamy następujące konstrukcje:
- silosy płaskodenne,
- silosy stożkowe,
- silosy cylindryczne,
- silosy na kołach
- silosy przystosowane do transportu.
Zalety silosów
Do głównych zalet korzystania z silosów zaliczyć można przede wszystkim możliwość przechowywania dużych ilości materiałów również tych wykazujących właściwości wybuchowe. Wówczas silosy dodatkowo wyposażone są w odpowiedni i efektywny system ochrony. Silosy są również łatwe w utrzymaniu i konserwacji oraz mogą być dostosowane do różnych potrzeb i wymagań. Ponadto, silosy pozwalają na łatwe zarządzanie ilością i jakością przechowywanego materiału.
Zabezpieczenie silosów
Silosy koniecznie trzeba zabezpieczać by uniknąć dużych strat ekonomicznych związanych z utratą produktu jak i samej instalacji. Jeżeli materiał jest łatwopalny i wybuchowy warto zwrócić uwagę na systemy zabezpieczeń przeciwwybchowych.
Silosy mogą być chronione za pomocą systemów „pasywnych” lub „aktywnych”. System ochronny dobiera się w oparciu o kilka czynników, m.in.: lokalizacja instalacji, wybuchowość pyłu, całkowity koszt utrzymania instalacji. Systemy pasywnej ochrony przeciwwybuchowej reagują na ciśnienie deflagracji, natomiast aktywna ochrona przeciwwybuchowa obejmuje elektroniczne wykrywanie i sterowanie, które aktywuje podłączone systemy w ciągu milisekund od wykrycia płomienia.
Na wyżej wspomniane systemy ochronne składają się produkty, takie jak np.: klapy przeciwwybuchowe/panele dekompresyjne, przerywacze ognia/bezpłomieniowe odciążanie wybuchu, butle HRD czy zawory przeciwwybuchowe. Wszystkie wspomniane systemy mają za zadanie zapobiec przede wszystkim wybuchowi, ochronić silos przed zniszczeniem lub jeśli nie z innych przyczyn nie jest to możliwe, ograniczyć jego skutki, odcinając i izolując propagację wybuchu.
- Zagrożenie pyłem i ryzyko zapłonu
- Rozwiązanie
- Odciążenie wybuchowe
- Tłumienie wybuchu
- Izolacja wybuchu
Zagrożenie pyłem i ryzyko zapłonu
Silosy są napełniane produktem za pomocą ciężarówki, cysterny, podnośnika kubełkowego lub przenośnika pneumatycznego. Wszystkie w/w sposoby mogą wytwarzać chmurę pyłu podczas procesu napełniania. Jeśli jedno z poniższych źródeł zapłonu dotrze do chmury pyłu, może nastąpić eksplozja:
- Elektrostatyczne „wyładowanie stożkowe” podczas napełniania.
- Iskry i żar dostające się do silosu podczas procesu napełniania.
- Tlący się, składowany produkt.
- Zanieczyszczony produkt np. elementami metalowymi.
Jeśli powstała fala ciśnienia wybuchu jest wyższa niż ciśnienie projektowe silosu, może dojść do katastrofalnych uszkodzeń zarówno urządzenia, jak i jego otoczenia, nie wspominając o samym produkcie. Ponadto, niezabezpieczone eksplozje mogą przedostać się do połączonych rur i zbiorników, powodując dodatkowe uszkodzenia – czasami bardziej niszczące niż początkowa deflagracja.
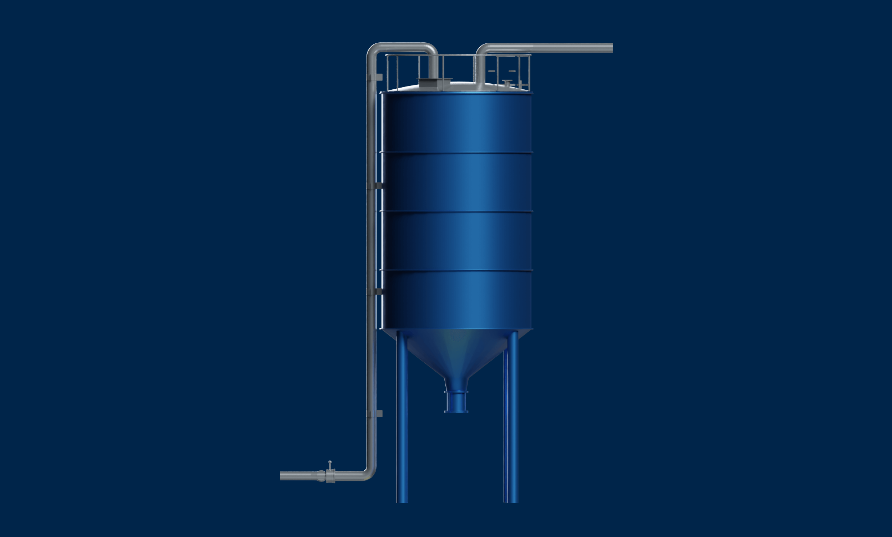
Rozwiązanie
Aby zmniejszyć ryzyko zapłonu w silosach, można zastosować odpowiednie zabezpieczenia oraz wprowadzić dobre praktyki organizacyjne. Niektóre z tych metod zapobiegania wybuchom mogą obejmować:
- Ograniczenie średnicy elektrycznej silosu poprzez wkładki przewodzące.
- Wykrywanie i gaszenie iskier lub płomieni na wlocie zapylonego powietrza i tłumienie lub izolowanie źródła przed wejściem do silosu.
- Monitorowanie tlenku węgla na dachu, a w razie wykrycia uwolnienie środka gaszącego.
- Systemy kontroli uziemienia rurociągu wlotowego do silosa.
- Kontrola załadunku surowca do silosa.
Ponieważ, jednak wyeliminowanie wszystkich potencjalnych źródeł zapłonu i pyłu zawieszonego w powietrzu wewnątrz silosów jest niemożliwe, systemy przeciwwybuchowe są wymagane zarówno dla ochrony pracowników, sprzętu i zachowania ciągłości procesu. Oczywiście jest to także wymóg związany z obowiązującymi przepisami prawnymi.
Metody ochrony przeciwwybuchowej mogą obejmować system aktywny, który wykorzystuje czujniki ciśnieniowe i optyczne, a następnie uruchamia urządzenia takie, jak butla tłumiąca wybuch HRD czy zawór szybkozamykający FAV. Skuteczną ochronę przeciwwybuchową gwarantują także systemy pasywne, w których klapy/panele przeciwwybuchowe i zawory izolujące wybuch (zawory przeciwwybuchowe) są uruchamiane przez falę ciśnienia generowaną przez sam wybuch.
Podczas, gdy rozwiązania pasywne są zazwyczaj bardziej opłacalne w instalacji i utrzymaniu, systemy aktywne tłumią wybuch w jego początkowej fazie, minimalizując szkody i obniżając ryzyko pożaru po zdarzeniu.
Niezależnie od typu systemu, każda strategia ochrony przeciwwybuchowej musi obejmować urządzenia chroniące przed początkową deflagracją zarówno silos, jak i urządzenia znajdujące się poniżej i powyżej (również przed wybuchami wtórnymi).
Zabezpieczenie zbiornika: Odciążenie wybuchu
W przypadku deflagracji, klapy/panele przeciwwybuchowe działają jako słaby punkt obudowy i zapewniają drogę ucieczki dla rosnącego ciśnienia i płomieni. Preferowane są klapy/panele przeciwwybuchowe zainstalowane na dachu silosu, aby zminimalizować wpływ na napełnianą objętość silosu.
Odpowietrzanie (dekompresja) wybuchowe jest stosunkowo tanie w porównaniu z innymi metodami ochrony i wymaga niewielkiej konserwacji. Konieczna jednak jest duża zewnętrzna strefa wyłączenia.
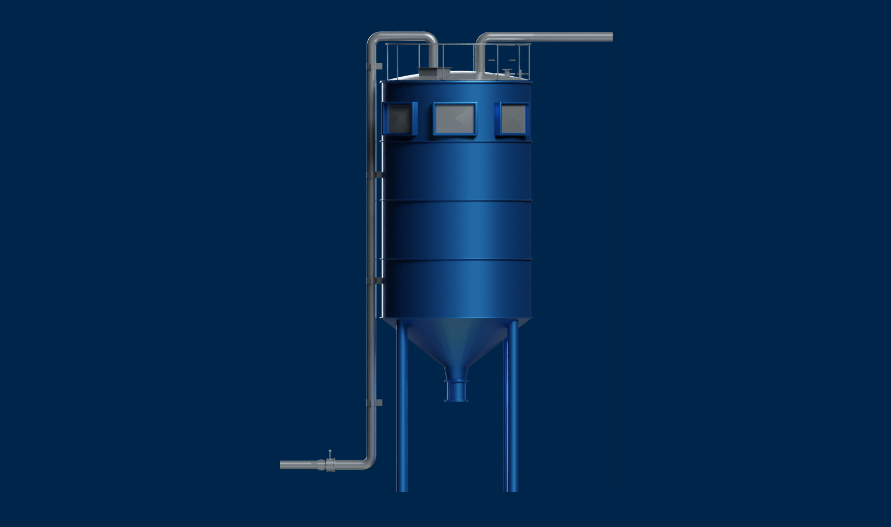
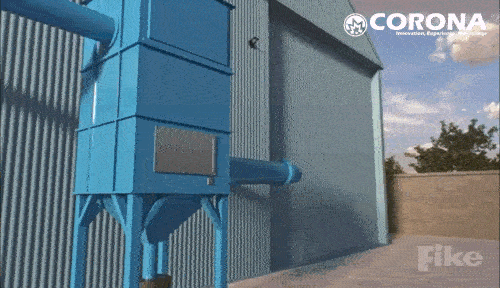
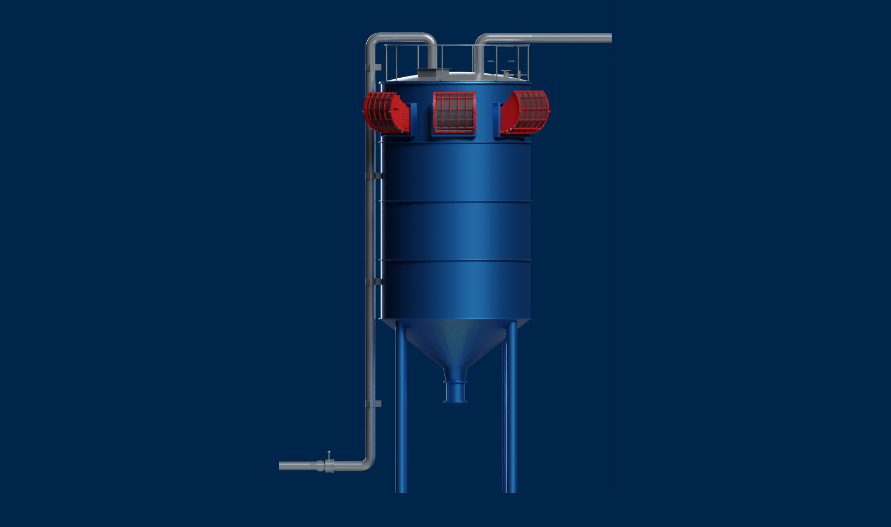
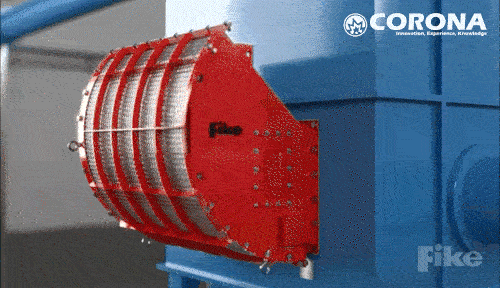
Jeśli wystarczająca zewnętrzna strefa wyłączenia nie jest dostępna lub gdy silos jest zainstalowany wewnątrz, opcjonalnym rozwiązaniem może być bezpłomieniowe odciążanie. Bezpłomieniowe urządzenie odciążające (przerywacz ognia) jest umieszczane nad klapą przeciwwybuchową i zawiera filtr płomieniowy, który gasi płomienie wybuchu. Zintegrowany filtr zatrzymujący pył zapobiega wydostawaniu się niespalonego materiału, co chroni przed wtórnymi wybuchami na zewnątrz silosu.
Dostępne są także dodatkowe akcesoria do klap/paneli przeciwwybuchowych, takie jak pokrywy pogodowe, które umożliwiają instalację nawet w najtrudniejszych warunkach atmosferycznych. Higieniczne klapy przeciwwybuchowe są również dostępne dla silosów służących do przechowywania żywności, w których stosuje się czyszczenie CIP.
Zabezpieczenie zbiornika: Tłumienie wybuchu
Podobnie jak w przypadku odsprzęgania wybuchu, systemy tłumienia wybuchu są również przeznaczone do łagodzenia wczesnej fazy deflagracji. Po wykryciu pierwszych stadiów deflagracji, butla HRD zostaje aktywowana i uwalnia środek/proszek tłumiący do silosu – wszystko odbywa się w bardzo krótkim czasie tzn. w ciągu kilku milisekund od zapłonu.
System tłumienia może być zalecany lub wręcz wymagany z następujących powodów:
- Gasi płomień wewnątrz silosu, zmniejszając potencjał szkód pożarowych.
- Eliminuje uwolnienie płomienia i znacznie zmniejsza ścieżkę ciśnienia związaną z odpowietrzeniem wybuchu.
- W znacznym stopniu eliminuje wydostawanie się toksycznych lub niebezpiecznych materiałów poza obudowę odpylacza.
- Znacząco ogranicza strefę zagrożenia wybuchem wokół urządzeń.
Butle tłumiące HRD są instalowane na dachu lub górnej ścianie bocznej i są równomiernie rozmieszczone, aby zapewnić dotarcie środka tłumiącego w postaci proszku do całej objętości silosu i zrównoważyć siły reakcji podczas aktywacji. Teleskopowe dysze rozpylające z odpornymi na ścieranie osłonami procesowymi są stosowane w celu ochrony przed erozją podczas napełniania i opróżniania silosu.
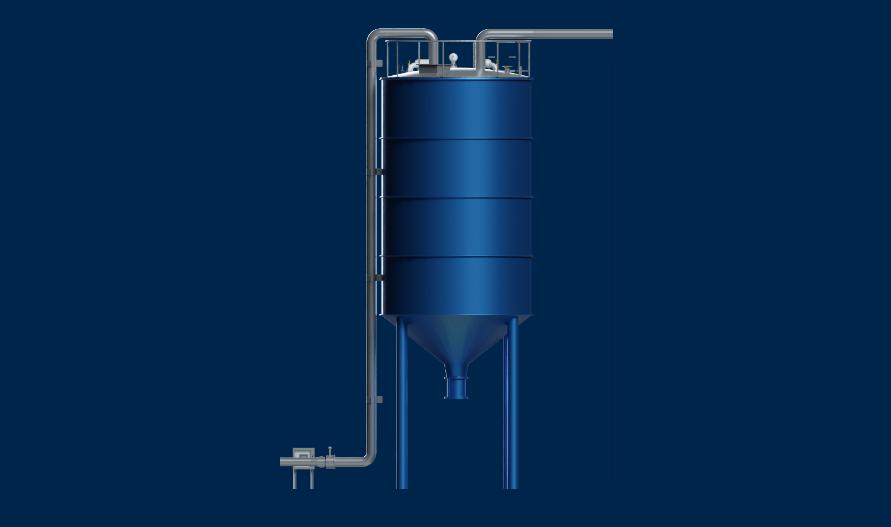
Ochrona podłączonego sprzętu: Izolacja wybuchu
Powstrzymanie eksplozji przed rozprzestrzenianiem się w górę i w dół do podłączonych rur i urządzeń jest równie ważne, jak powstrzymanie początkowej deflagracji.
Dopuszczenie do rozprzestrzenienia się płomienia na połączone zbiorniki może prowadzić do spiętrzenia ciśnienia. Następująca deflagracja w naczyniu połączonym rozpoczyna się przy zwiększonym ciśnieniu i ma poważniejsze konsekwencje, zarówno pod względem szybkości spalania, jak i ciśnienia końcowego.
Wlot produktu (linia napełniania pneumatycznego i linia napełniania grawitacyjnego) jest często chroniony aktywnymi barierami mechanicznymi, ponieważ pasywne bariery mechaniczne są zagrożone zatkaniem ze względu na duże ilości produktu przenoszonego do silosu. Izolacja chemiczna może być również stosowana, jeśli objętość silosu nie przekracza limitów tej bariery chemicznej.
Jeśli zainstalowana jest linia odpylania, może być ona izolowana za pomocą różnych metod ochrony, w tym zaworu zwrotnego, zasuwy lub bariery chemicznej.
Wylot produktu może nie wymagać ochrony, jeśli dozownik celkowy jest zatwierdzony przez stronę trzecią jako urządzenie izolujące przed wybuchem i aktywuje się wystarczająco szybko po wykryciu wybuchu. Jeśli dozownik celkowy nie jest w stanie odizolować się od wybuchu, może być zalecany system ochrony aktywnej tzn. butla SRD, zakładając, że w kanale jest wystarczająco dużo miejsca.
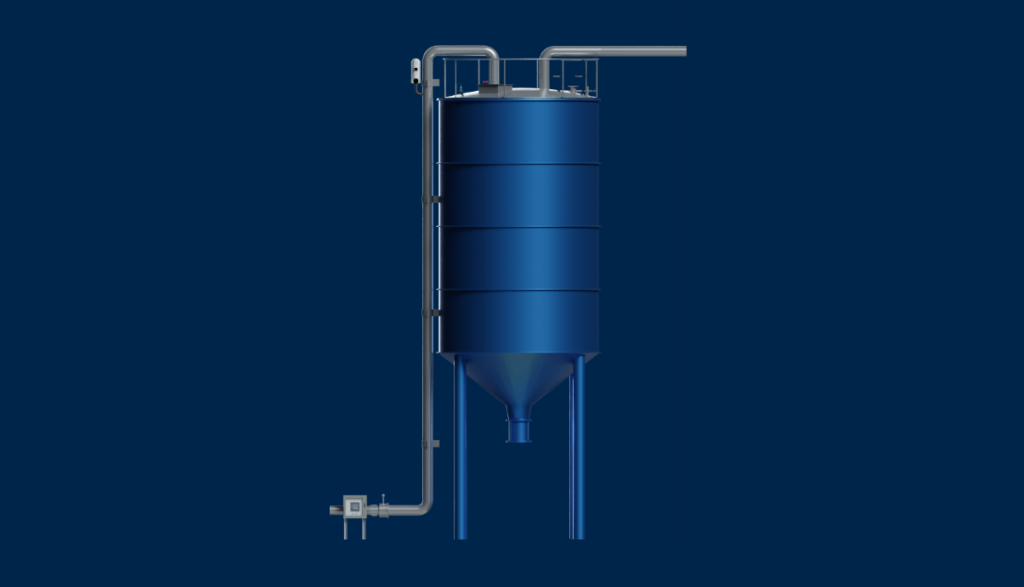