Wherever flammable liquids, gases or vapors are transported and stored, flame arresters should be in use. This will minimize the risk when explosive media ignite and protect the factory, the installation and, most importantly, people.
It is recommended that all equipment that has permanent sources of ignition be equipped with flame arresters.
Tanks and mixers often, as a rule, have breather valves or appropriate vents installed, which, through the potential danger of contact with an ignition source, can lead to an explosion. It is therefore recommended in modern industry to protect such processes with flame arresters.
Flame arresters belong to passive deflagration and detonation protection systems and have no moving parts. The basis of the construction of each flame arrester is a properly torqued and arranged piece of braided metal, which by its properties guarantees the operation of the device.
The consequences of the slightest spark in an installation can be horrific. Devastation and destruction is usually the picture that shows up after a deflagration or detonation in installations where potentially dangerous explosive gases or vapors are transported. Once the gas in the containment is ignited, the flame begins to move through the pipeline with incredible speed, resulting in devastating force. The average speed at which the flame begins to move is 3000 m/s.
For such tasks we have prepared our Valwo flame arrester, which will stop the flame, cool it down properly and protect the entire installation and everything around it.
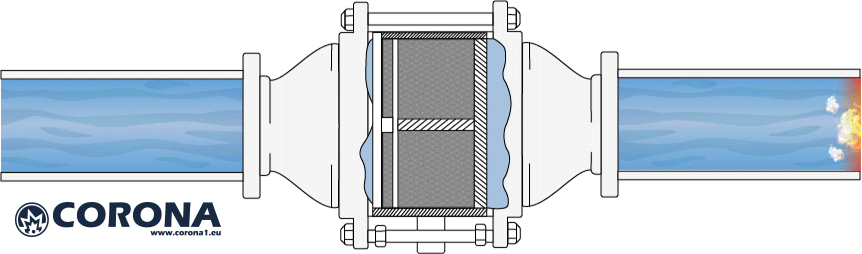
Depending on the application, we offer suitable flame arresters for a special product or application. There is a possible combination: flame arrester with breathing valve or vacuum valves alone or overpressure valves.
Each gas has its own characteristics. Based on it, it is possible to select the appropriate cross-section of braided metals through which the flame will not pass. This behavior is determined by the selection and manufacture of a fire fuse with appropriate gaps called MESG for short. (Maximum Experimental Safe Gap).
In order to adequately smother and cool the flame so that it does not penetrate further, the slots must be properly selected so that the MESG parameters do not exceed those of the medium.
Not only the height of the element is important, but also its length. It must be calculated so that it absorbs the heat of the explosion in an appropriate manner. In this way, after the gas passes through the entire element at the end, the temperature of the gas will be below its auto-ignition temperature, thus protecting everything behind the flame arrester.
Technical parameters:
- size range from DN 6 to DN 600
- maximum working temperature up to 250°C
- certified for high operating pressures
- Types of flame arresters:
Types of flame arresters:
- deflagration, detonation, short burning and long burning
- linear flame arresters for pipelines – mounted as components of a pipeline transporting gases or vapors of flammable liquids
- liquid flame arresters – used to protect storage tanks from vapor explosion, mounted on the pipeline filling (hydraulic closure) and emptying the tank (foot valve)
- final flame arrester – vent/vent valve used to ensure uninterrupted flow of air into the tank and outflow of gases to the atmosphere while protecting the tank from flame back. Protection is made possible by the use of a special explosion-proof insert with slots adapted to the explosion group of the medium stored in the tank