At almost every branch of modern industry polymeric materials are used. They undergo wearing while exploating, so maintenance is conducted. A significant load of knowledge is involved to recognize the type of polymeric material, due to select adequate solvent, glue or lacquer for processing stage. In the case of total destruction, materials are disposed of, which involves a huge amount of wastes – from disposable packagings, to everyday life objects and machinery or constructional parts.
A special solution for transformation of polymeric materials has been developed, as they don’t decay rapidly. Also a landfill site are of limited capacity. The solution is pelletizing system.
A granulate of artificial materials is widely applied in many processing plants, where single screw extruder plasticizing systems are involved (equal rods of polymeric materials are obtained).
As far as pelletizing system is concerned, rheological and thermal properties, efficiency of electricity consumption, process reliability, further performance of granulate and durability of device must be considered.
SPHERO®
Underwater pelletizing systems for highly profi table throughput rates of up to 36,000 kg per hour
The SPHERO® underwater pelletizing system has been particularly designed to process thermoplastics and produces spherical pellets. This most flexible system is applied in the production of raw materials, compounds, masterbatches, engineering plastics, wood polymer composites, thermoplastics elasto-mers, hot-melt adhesives, and in the field of recycling.
SPHERO® – Your benefits:
- Outstanding pellet quality
- Increased production efficiency
- Enhanced process reliability
- Optimal access
- Convenient and safe operation
- Quick product change
- Pelletizing of specialized products
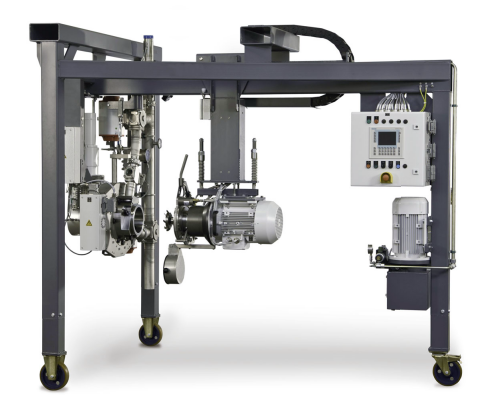
M-USG®
The M-USG® underwater pelletizing strand system has been producing virgin polymers all over the world for decades. The extremely flexible system guarantees a high level of system availability, especially in continuous operation, and fulfills the very highest demands in terms of cylindrical pellet quality.
M-USG® – Your benefits:
- Outstanding, constant pellet quality
- Throughputs up to 20,000 kg/h
- Increased degree of system availability thanks to quick-change cutting head
- High level of automation
- Long service life of extremly wear-resistant cutting tools
- Easy accessibility – user-friendly for operation and maintenance
- Most reliable
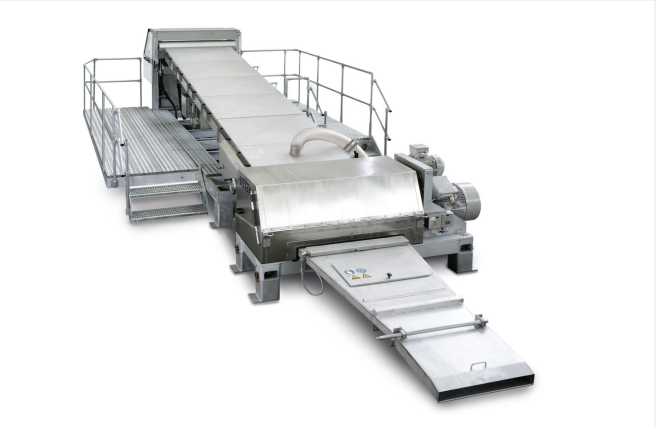
P-USG®
The P-USG® underwater strand pelletizing systems made by Automatik Plastics Machinery have been particularly designed for both the production of virgin polymers with lower throughput rates and for recycling applica-tions. The simple design of the machine stands for engineering reduced to the essentials while heading for high process stability and pellet quality.
P-USG® – Your benefits:
- Consistent outstanding pellet quality
- Simple operation
- Automatic strand lacing on start-up and during production
- Operating speeds up to 250 m/min
- Excellent quality of the feed tools and cutting tools
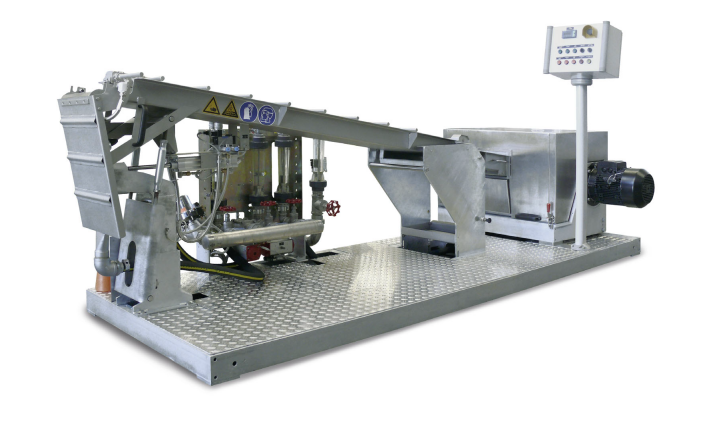
BAOMO®
The application of BAOMO® strand pelletizers is higly recommended for laboratories and for the production of small runs. The typical characteristic is the cantilever bearing of all elements in the cutting chamber. These are easily accessible for maintenance, adjustment and cleaning.
BAOMO® – Your benefits:
- Cantilevered design results in easy access for cleaning and maintenance
- Several options available, e.g. cutting tools and wear protection
- Attractive cost-performance ration
- Short delivery time
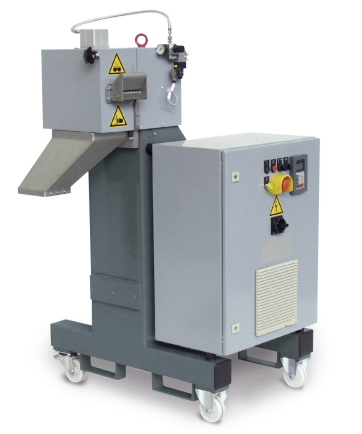
PRIMO-S®
The strand pelletizers of the PRIMO-S® series are characterized by high flexibility and very good machine availability with maximum efficiency. As an allrounder or machine specially adapted to your product, the PRIMO-S® produces cylindrical pellets of excellent quality
PRIMO-S® – Your benefits:
- Shortest possible unguided section from feeding unit to cutting unit
- Sturdy, double-sided bearing of the cutting rotor
- Very high system availability due to wear-resistant cutting tools
- Quick and easy access for cleaning and servicing; quick product changeover
- Consistent pellet quality
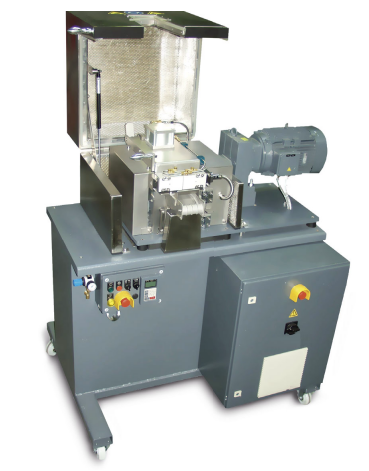
PRIMO PLUS®
The dry cut pelletizers of the PRIMO PLUS® Series are characterised by their robust design. The double-sided bearing of the cutting rotor ensures high stability and precision, resulting in excellent quality of the cylinder pellets. Wear-protected machine parts alsoensure a high degree of machine availability and profitability.
PRIMO PLUS® – Your benefits:
- Shortest possible unguided section from feeding unit to cutting unit
- Sturdy, double-sided bearing of the cutting rotor to meet highest stability and precision standards
- Upper feed roll driven available
- Changes on the pellet length and weight to be made with Dual Drive
- Integration into automatic JSG system feasible
- Very high machine availability due to wear-resistant cutting tools
- Quick and easy access for cleaning and servicing; quick product changeover
- Use of a hybrid rotor with 200 mm diameter possible

DROPPO®
The DROPPO® drop pelletizing system made by Automatik Plastics Machinery has been particularly designed for the production of perfectly uniform, dust-free pellets. The cool-ing and solidifi cation process may use air, nitrogen, or water – thus offering utmost flexibility to the customer.
DROPPO® – Your benefits:
- Ideally suited for low-viscosity melts and liquids
- Perfectly spherical, dust-free pellets ensure superb conveyance and high bulk-density storage as well as precise dosing during subse-quent processing
- Drop process unit may be integrated into already existing lines such as spray towers, etc.
- High profi tability due to reduced energy consumption and low manpower requirements
- Quick and simple product changeover
- No mechanical wear
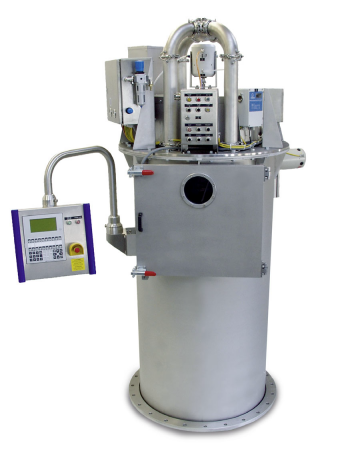